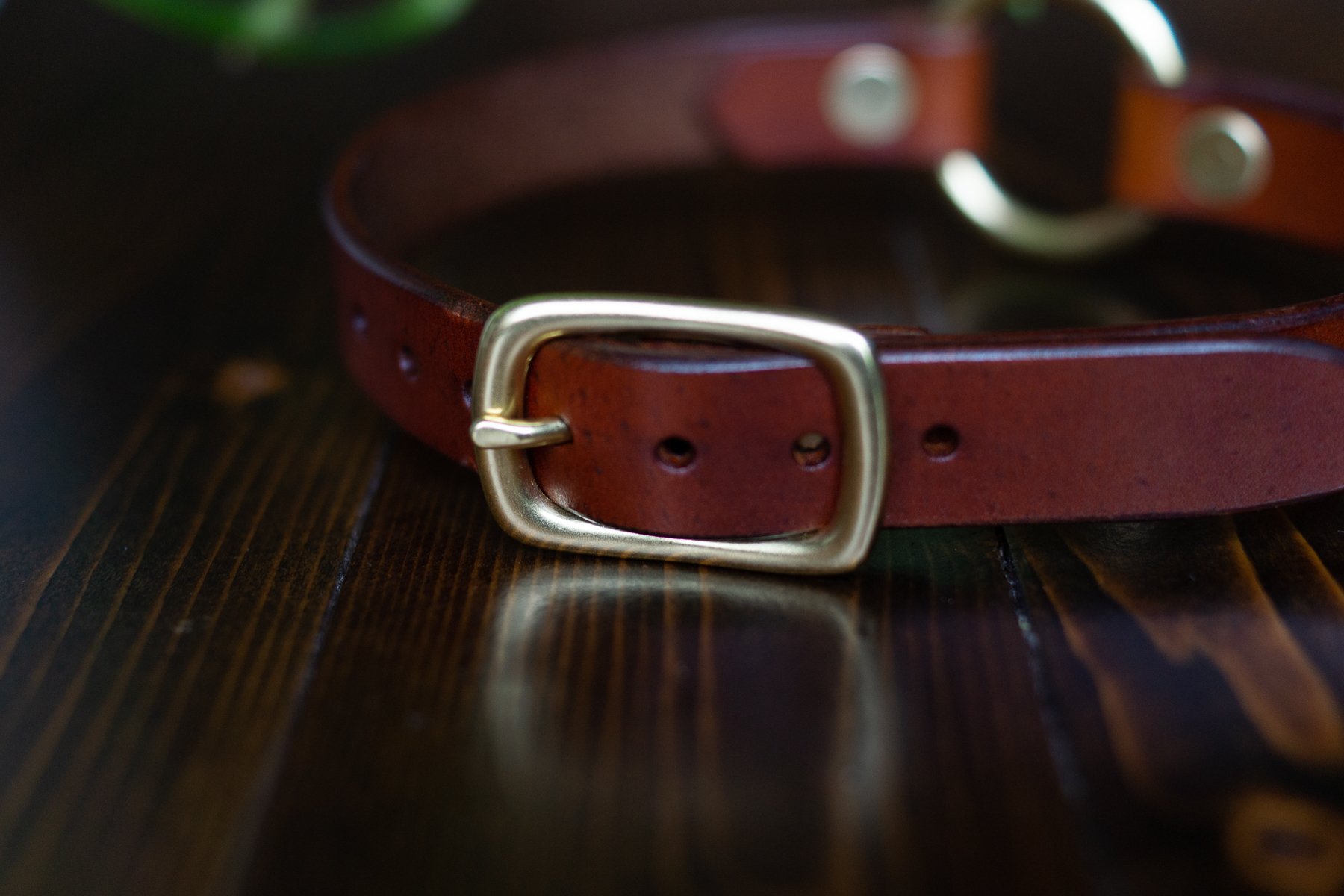
Frequently Asked Questions
Why is your work so expensive? I can find leather pieces for half the price on Etsy!
The main determining factors for the prices of my pieces are:
Cost of materials. I use high quality materials, including heavy solid brass hardware and premium grade responsibly-sourced natural vegetable-tanned leather.
Time investment. All of my pieces are, from start to finish, 100% hand made. I cut every piece of leather; I hand dye all of it, often with bespoke color blends; I do all of the stitching without a machine; I sand and polish the edges; I punch every hole and hammer every rivet. I carefully apply oils and finishes. I have no employees, no assistants, no partners, and no machines (except for one tabletop sander that I can use on some longer edges). All of which to say, it takes me a long time to create my pieces. The return from my sales usually doesn’t come close to approaching minimum wage for the time investment.
Furthermore, every bit of money from my sales is reinvested into tools & supplies for future projects. I hope to one day actually make a small profit from this work, but for now the best-case scenario is usually to break even.
There are many cheaper leather pieces available online. Many of these even made by craftspeople as good or better than I am! Those pieces are typically made with cheaper materials, less attention to detail, and/or the artists are drastically undervaluing their work.
Ultimately, my position is that I believe it is a good thing that you, as a potential buyer of leather goods, have a variety of choices. It is a very good thing for low-income folks (like myself) to have access to nice things! And if you want to, and have the ability to, spend a little more to invest in something nice, and to support an artist whose work you appreciate, that is good too!
Also - online shopping platforms drive prices up in multiple ways. Etsy, for example, takes a variable cut, depending on a few factors. Usually it ends up being about 10%. They also will effectively bury your listings unless you agree to offer free shipping, which can end up being a significant percentage loss depending on distance and the size of the item. All of this means that in order to not sell at a loss, I need to mark item prices up by about 15-20% on those platforms.
This is why I encourage anyone interested in buying a Möbius Leatherworks piece to CONTACT ME directly! I can often offer a better price on products when dealing directly with a prospective customer.
What kinds of materials do you use and why?
Whenever possible, I use almost exclusively solid brass hardware, for its durability and resistance to rust. Brass is low maintenance and ages gracefully, developing a nice patina over time. It is harder and stronger than copper or aluminum, and unlike stainless steel, will never rust.
Due to the weight of high quality brass hardware, I also prefer to use thick, heavy leather. Expect the leather in most of my pieces to be heavier and firmer than most commercial leather products. Another benefit of this is superior durability and longevity.
I also prefer to use raw, natural vegetable-tanned leather. Pre-colored chrome-tanned leathers, which dominate the commercial leather product industry, are generally easier to work with and faster to produce products from, since it removes several steps from the making process. However, for myself as a maker, I prefer to have a hand in as many of those processes as possible. Turning a roll of raw, natural leather into finished work is more rewarding to me than buying sheets of pre-finished leather and simply assembling it (not that there’s anything wrong with doing so, its simply not my preference).
Vegetable-tanned leather is also safer and more environmentally friendly than chrome tanning, which relies on highly toxic chemical processes.
Where does your leather come from? Is it ethically and environmentally sourced?
Most of my early works - including many pieces shown on this site - are made from leather I acquired locally from longtime Portland mainstay, Oregon Leather Company. I am proud to have the opportunity to support a local business that has served downtown Portland and Eugene, Oregon for over 100 years.
Moving forward, knowing as much as possible about the source of the leather I work with is something that is becoming increasingly important to me as a craftsperson. I am currently working primarily with leather from Hermann Oak Leather, often touted as amongst the highest quality leather producers available. Significantly, their leather is also responsibly sourced from byproduct of the US beef industry, and never comes from animals raised or killed for leather. If these excess hides were not repurposed for leather, they would be sent to landfills. Furthermore, the costs of the hides accounts for such a small percentage of the overall commercial value of the animal, it has virtually no effect on the number of cattle raised for beef.
Why not work with vegan leather?
First and foremost, I am not vegan. I respect the lifestyle choice of vegans, and admire any commitment to living a more ethical and environmentally responsible existence. Veganism is, however, just one choice an individual can make towards that end, and no person can be expected to lead an ethically or environmentally perfect life. So we all choose our own battles to fight, and veganism is not one of mine. Furthermore, in the present day late-stage capitalist United States, a fully vegan lifestyle is not a widely accessible option for many folks.
There is a lot of debate about the comparative environmental impacts of animal leather vs vegan “leather.” There isn’t a single straightforward answer to the question of which is better or worse. Part of that is due to the fact that there are many products that can fall under the umbrella of “vegan leather.” Some of these are environmentally friendly, biodegradable, and plant-based products. Most are not.
Most substances commonly referred to as “vegan leather” are essentially plastics, the production and eventual disposal of which can have highly detrimental environmental impacts. Chemical-based plastic products masquerading as “vegan leather” can last for hundreds of years in landfills. However, in fairness, the supposed biodegradability of animal leather is also often highly overstated. The tanning process is specifically designed to slow the natural processes of bio-degradation. The cattle industry is also extremely damaging to the environment, and if you compare the estimated impact of one single cow’s worth of leather vs an equivalent quantity of plastic-based vegan product, the potential impact of the animal product is almost certainly higher.
However. Responsibly sourced animal leather is entirely a byproduct of the meat industry. The impact of cattle factory-farming falls squarely on the shoulders of the beef industry. The hides of the animals that are raised and killed for meat would otherwise go directly to landfills, and the profit from selling the hides to tanneries is low enough that it has no influence on quantities of animals being produced. Therefore, it is an unfair false equivalency to consider the environmental impact of the large-scale cattle industry in any direct comparisons between the relative impact of animal leather vs vegan plastic production.
That said, the animal leather components of the large-scale fast fashion mega industries are, of course, environmentally and ethically reprehensible. As are pretty much every aspect of those industries. Reducing as much as possible your consumption of fast fashion products - be they animal, plastic, or otherwise - is one of the most ethically significant steps we can all take.
As in all things, the real villain is of course, Capitalism.
How do I care for and clean my new leather piece?
Most of the leather products I make will be very low maintenance. Everything I make is conditioned with 100% pure Neatsfoot oil, which should keep it safe from drying out too quickly. In general, leather pieces that see frequent use, and especially frequent exposure to the elements, can and should be occasionally conditioned with a similar oil or leather conditioner product. The ideal frequency of such treatment can vary depending on context. With something high use and high exposure, like a pair of boots, I will apply a conditioner every four to six weeks. Some pieces will require considerably less. Most of the pieces I make will not require very much treatment; but a good rule of thumb is that if something looks or feels like its beginning to dry out or feel stiff, it might be time to apply a bit of oil with a dry, clean cloth.
Its also worth noting that many of my wearable products, if designed to be worn potentially in close contact with clothing or other fabrics, are topcoated with a resolene finish (to minimize possible color transfer). This coating does make it harder for the leather to absorb new oils and conditioners. But it also should help prevent the leather from drying out in the first place.
The leather can generally be cleaned by wiping with a dry or damp cloth, then wiped dry. Never dry wet or damp leather with a heater or blow-dryer.
Do you do custom projects? How can I place a custom order?
Broadly speaking, I am not currently taking on custom projects for the time being, though I may consider exceptions in some circumstances. I will always give consideration to requests about specific sizing or accessibility concerns (I can’t guarantee I’ll be able to take the project on, but I will be happy to discuss it and try to figure something out).
Beyond that, I simply don’t have the time or bandwidth for custom projects currently. I have decided to invest the crafting time that I do have these days into working on projects that will nourish my passion for the craft and contribute to growing my skills.
Please don’t hesitate to Contact Me with any questions or inquiries you might have.